Основные ссылки
|
ГОСТ Р 50838-95* Трубы из полиэтилена для газопроводов. Технические условия.
23 ГИДРАВЛИЧЕСКИЕ И
ПНЕВМАТИЧЕСКИЕ СИСТЕМЫ И
КОМПОНЕНТЫ ОБЩЕГО НАЗНАЧЕНИЯ
ОКС 23.040.20,
83.140.30
Группа Л26
Изменение
№ 3 ГОСТ Р 50838-95 Трубы из полиэтилена для газопроводов.
Технические условия
Утверждено
и введено в действие Приказом Федерального агентства по техническому
регулированию и метрологии от 28.09.2004 № 17-ст
Дата введения
2005-01-01
Раздел
2 дополнить ссылками:
«ГОСТ
17.2.3.02—78 Охрана природы. Атмосфера. Правила установления допустимых
выбросов вредных веществ промышленными предприятиями
ГОСТ
12162—77 Двуокись углерода твердая. Технические условия
ГОСТ
28084—89 Жидкости охлаждающие низкозамерзающие. Общие технические условия
ГОСТ
29325-92 (ИСО 3126-74) Трубы из пластмасс. Определение размеров».
Пункт
3.1.3 изложить в новой редакции:
«3.1.3 коэффициент
запаса прочности С≥2,0 выбирают при проектировании
газораспределительных трубопроводов с учетом условий эксплуатации (приложение
А)».
Пункт
4.1. Таблицу 1 изложить в новой редакции
Таблица
1
В миллиметрах
Наружный диаметр
|
SDR 17,6
|
SDR
17
|
SDR
13,6
|
SDR
11
|
SDR 9
|
Овальность после экструзии,
не более
|
Толщина стенки
|
Номин.
|
Пред. откл. среднего
наружного диаметра
|
Номин.
|
Пред. откл.
|
Номин.
|
Пред. откл.
|
Номин.
|
Пред. откл.
|
Номин.
|
Пред. откл.
|
Номин.
|
Пред. откл.
|
20
|
+0,3
|
-
|
-
|
-
|
-
|
-
|
-
|
2,3*
|
+0,4
|
3,0*
|
+0,4
|
1,2
|
25
|
+0,3
|
-
|
-
|
-
|
-
|
-
|
-
|
2,3
|
+0,4
|
3,0*
|
+0,4
|
1,2
|
32
|
+0,3
|
-
|
-
|
-
|
-
|
2,4
|
+0,4
|
3,0
|
+0,4
|
3,6
|
+0,5
|
1,3
|
40
|
+0,4
|
2,3
|
+0,4
|
2,4
|
+0,4
|
3,0
|
+0,4
|
3,7
|
+0,5
|
4,5
|
+0,6
|
1,4
|
50
|
+0,4
|
2,9
|
+0,4
|
3,0
|
+0,4
|
3,7
|
+0,5
|
4,6
|
+0,6
|
5,6
|
+0,7
|
1,4
|
63
|
+0,4
|
3,6
|
+0,5
|
3,8
|
+0,5
|
4,7
|
+0,6
|
5,8
|
+0,7
|
7,1
|
+0,8
|
1,5
|
75
|
+0,5
|
4,3
|
+0,6
|
4,5
|
+0,6
|
5,6
|
+0,7
|
6,8
|
+0,8
|
8,4
|
+1,0
|
1,6
|
90
|
+0,6
|
5,2
|
+0,7
|
5,4
|
+0,7
|
6,7
|
+0,8
|
8,2
|
+1,0
|
10,1
|
+1,2
|
1,8
|
110
|
+0,7
|
6,3
|
+0,8
|
6,6
|
+0,8
|
8,1
|
+1,0
|
10,0
|
+1,1
|
12,3
|
+1,4
|
2,2
|
125
|
+0,8
|
7,1
|
+0,9
|
7,4
|
+0,9
|
9,2
|
+1,1
|
11,4
|
+1,3
|
14,0
|
+1,5
|
2,5
|
140
|
+0,9
|
8,0
|
+0,9
|
8,3
|
+1,0
|
10,3
|
+1,2
|
12,7
|
+1,4
|
15,7
|
+1,7
|
2,8
|
160
|
+1,0
|
9,1
|
+1,1
|
9,5
|
+1,1
|
11,8
|
+1,3
|
14,6
|
+1,6
|
17,9
|
+1,9
|
3,2
|
180
|
+1,1
|
10,3
|
+1,2
|
10,7
|
+1,2
|
13,3
|
+1,5
|
16,4
|
+1,8
|
20,1
|
+2,2
|
3,6
|
200
|
+1,2
|
11,4
|
+1,3
|
11,9
|
+1,3
|
14,7
|
+1,6
|
18,2
|
+2,0
|
22,4
|
+2,4
|
4,0
|
225
|
+1,4
|
12,8
|
+1,4
|
13,4
|
+1,5
|
16,6
|
+1,8
|
20,5
|
+2,2
|
25,2
|
+2,7
|
4,5
|
250
|
+1,5
|
14,2
|
+1,6
|
14,8
|
+1,6
|
18,4
|
+2,0
|
22,7
|
+2,4
|
27,9
|
+2,9
|
5,0
|
280
|
+1,7
|
15,9
|
+1,7
|
16,6
|
+1,8
|
20,6
|
+2,2
|
25,4
|
+2,7
|
31,3
|
+3,3
|
9,8
|
315
|
+1,9
|
17,9
|
+1,9
|
18,7
|
+2,0
|
23,2
|
+2,5
|
28,6
|
+3,0
|
35,2
|
+3,7
|
11,1
|
* Расчетное значение толщины стенки округлено до
2,3 мм для SDR 11 и до 3,0 мм для SDR 9.
Примечание – Номинальный наружный диаметр
соответствует минимальному среднему наружному диаметру.
|
Пункт
4.2. Первый абзац. Заменить значения: «200 и 225 мм» на «200 мм и более»;
дополнить
абзацем:
«Расчетная
масса приведена в приложении В».
Пункт
5.2. Таблица 2. Графа «Значение показателя для труб из». Для показателя 1
второй абзац после слова «желтый» дополнить словами: «(оттенки не
регламентируются)»;
показатель
9 изложить в новой редакции; таблицу дополнить примечанием:
Наименование показателя
|
Значение показателя для
труб из
|
Метод
испытания
|
ПЭ80
|
ПЭ100
|
9 Стойкость к быстрому
распространению трещин при 0 °С при максимальном рабочем давлении
трубопровода более 0,4 МПа для труб диаметром 90 мм и более:
|
|
|
|
9.1 маломасштабный метод,
критическое давление, МПа, не менее
или
|

|

|
По 8.10
|
9.2 полномасштабный метод,
критическое давление, МПа, не менее
|
МОР´1,5
|
МОР´1,5
|
По 8.12
|
Примечание — Для расчета
критического давления по показателям 9.1 и 9.2 принимают максимальное
значение МОР по таблице А.1 для труб выбранного SDR и типа полиэтилена.
|
Пункт
5.3.1 изложить в новой редакции:
«5.3.1
Маркировку наносят на поверхность трубы методом термотиснения, методом
термотиснения с окрашиванием наносимого тиснения, методом цветной печати или
другим способом, не ухудшающим качество трубы, с интервалом не более 1 м.
Маркировка должна включать последовательно: наименование
предприятия-изготовителя и/или товарный знак, условное обозначение трубы без
слова «труба», месяц и год изготовления. В маркировку допускается включать
другую информацию, например, наименование страны и номер партии.
Глубина
тиснения — не более 0,3 мм для труб номинальной толщиной стенки до 6,8 мм
включительно и не более 0,7 мм для труб с номинальной толщиной стенки более 6,8
мм. При маркировке труб методом цветной печати глубину тиснения не
контролируют».
Пункты
5.4—5.4.3 изложить в новой редакции (пункт 5.4.4 исключить):
«5.4
Упаковка
5.4.1
Трубы диаметром 225 мм и менее, выпускаемые в отрезках, связывают в пакеты
массой до 3 т, скрепляя их не менее чем в двух местах таким образом, чтобы
расстояние между местами скрепления было от 2,0 до 2,5 м, а для пакетов труб,
предназначенных для районов Крайнего Севера и приравненных к ним местностей, —
от 1,0 до 1,5 м. Допускается по согласованию с потребителем трубы в отрезках не
упаковывать.
Трубы
диаметром более 225 мм в пакеты не связывают.
5.4.2
Бухты скрепляют не менее чем в четырех местах, а для районов Крайнего Севера и
приравненных к ним местностей — не менее чем в шести местах.
При
упаковке труб в бухты и на катушки концы труб должны быть заглушены и жестко
закреплены. Внутренний диаметр бухты должен быть не менее 20 наружных диаметров
трубы.
5.4.3
При упаковке труб используют средства по ГОСТ
21650 или другие, не ухудшающие качество поверхности труб».
Пункт
6.5 дополнить абзацем (перед первым):
«Для
предотвращения загрязнения атмосферы в процессе производства труб необходимо
выполнять требования ГОСТ
17.2.3.02».
Пункт
7.1. Первый абзац. Исключить слова: «или партии»;
последний
абзац. Заменить значения: «180—225 мм» на «180 мм и более».
Пункты
7.2—7.4 изложить в новой редакции:
«7.2
Для определения соответствия качества труб показателям таблицы 3 проводят
приемосдаточные и периодические испытания.
Отбор
проб для испытаний проводят равномерно в течение производства. Для определения
овальности после экструзии по требованию потребителя пробы отбирают у
изготовителя на выходе с технологической линии и перед намоткой труб в бухты,
катушки.
В
случае разногласий отбор проб от партии проводят методом случайной выборки.
Для
проведения испытаний труб (кроме приемосдаточных) выбирают по одному типовому
представителю из каждой группы труб по номинальному наружному диаметру: группа
1—75 мм и менее, группа 2 — от 90 до 200 мм, группа 3—225 мм и более.
Результаты испытаний распространяются на всю группу диаметров с любым
стандартным размерным отношением SDR.
Таблица
3
Наименование показателя
|
Частота контроля
|
Объем выборки
|
1 Внешний вид поверхности
|
На каждой партии
|
5 проб
|
2 Размеры
|
|
5 проб
|
3 Относительное удлинение
при разрыве
|
»
|
5 проб
|
4 Изменение длины труб
после прогрева
|
1
раз в 6 мес. на одном диаметре от каждой группы, при этом каждый диаметр
контролируют не реже 1 раза в 2 года
|
3 пробы
|
5 Стойкость при постоянном
внутреннем давлении (20º С - 100 ч)
|
1
раз в 3 мес. на одном диаметре от каждой группы, при этом каждый диаметр
контролируют не реже 1 раза в 2 года
|
3 пробы
|
6 Стойкость при постоянном
внутреннем давлении (80º С - 165 ч)
|
1
раз в 3 мес. на одном диаметре от каждой группы, при этом каждый диаметр
контролируют не реже 1 раза в 2 года
|
3 пробы
|
7 Стойкость при постоянном
внутреннем давлении (80º С -1000
ч)
|
1
раз в 6 мес. на одном диаметре от каждой группы, при этом каждый диаметр
контролируют не реже 1 раза в 3 года
|
1 проба*
|
8 Стойкость к газовым
составляющим
|
1
раз в 3 года на трубах диаметром 32 мм с SDR 11
|
3 пробы
|
9 Термостабильность труб
|
1
раз в 12 мес. на одном диаметре от каждой группы, при этом каждый диаметр
контролируют не реже 1 раза в 2 года
|
2 пробы
|
10 Стойкость к быстрому
распространению трещин
|
|
|
10.1 маломасштабный метод
или
|
1
раз в 12 мес. на одном диаметре от групп 2 и 3
|
3 пробы
|
10.2 полномасштабный метод
|
1
раз в 12 мес. на одном диаметре от групп 2 и 3
|
2 пробы
|
11 Стойкость к медленному
распространению трещин
|
1
раз в 12 мес. на одном диаметре от каждой группы
|
1 проба*
|
* В случае разногласий по
показателям 7 и 11 от партии отбирают 2 пробы.
Примечание — Испытания по показателям
4—11 проводят на каждой марке сырья.
|
7.3 При
получении неудовлетворительных результатов приемосдаточных испытаний хотя бы по
одному показателю по нему проводят повторные испытания на удвоенной выборке. При
получении неудовлетворительных результатов повторных приемосдаточных испытаний
партию труб бракуют.
7.4 При
получении неудовлетворительных результатов периодических испытаний хотя бы по
одному показателю, кроме показателя «стойкость к быстрому распространению
трещин», по нему проводят повторные испытания на удвоенной выборке. При
получении неудовлетворительных результатов повторных периодических испытаний их
переводят в категорию приемосдаточных испытаний до получения положительных
результатов по данному показателю.
При
получении неудовлетворительного результата по показателю «стойкость к быстрому
распространению трещин» по маломасштабному методу проводят испытания
полномасштабным методом на трубах из сырья той же марки, того же изготовителя.
При
получении неудовлетворительного результата по полномасштабному методу трубы
могут быть использованы на максимальное рабочее давление 0,4 МПа или должны
быть испытаны при давлении, рассчитанном для меньшего значения МОР по таблице
А.1».
Пункт
8.3. Заменить слово: «клеймения» на «тиснения».
Пункт
8.4.3. Первый абзац после слов «в одном сечении» дополнить словами: «по ГОСТ
29325».
Пункт
8.4.4 изложить в новой редакции:
«8.4.4
Толщину стенки труб е определяют по ГОСТ 29325 с обоих торцов каждой
пробы не менее чем в шести точках, равномерно расположенных по периметру
образца на расстоянии не менее 10 мм от торца.
Измерения
проводят для труб номинальной толщиной до 25 мм включительно— микрометром типа
МТ или стенкомером, более 25 мм — микрометром типа МК. Полученные значения
толщины стенки должны соответствовать указанным в таблице 1».
Пункт
8.4.5. Второй абзац дополнить словами: «или по показаниям счетчика метража в
процессе производства. В случае разногласий измерения проводят рулеткой»;
третий
абзац исключить.
Пункты
8.4.6, 8.5 изложить в новой редакции:
«8.4.6
Овальность трубы после экструзии определяют как разность между максимальным и
минимальным наружными диаметрами, измеренными по ГОСТ 29325 в одном сечении
пробы штангенциркулем или микрометром типа МК.
8.5
Относительное удлинение при разрыве определяют по ГОСТ 11262, при этом
толщина образца должна быть равна толщине стенки трубы, а за результат
испытания принимают минимальное значение из пяти определений, округленное до
двух значащих цифр.
Пять
образцов лопаток изготовляют из проб, отобранных по 7.2, причем из каждой пробы
изготовляют один образец.
Тип
образца-лопатки, способ изготовления и скорость испытания выбирают в соответствии
с таблицей 4.
Таблица
4
Номинальная толщина стенки
трубы е, мм
|
Тип образца-лопатки по
ГОСТ 11262
|
Способ изготовления
|
Скорость испытания, мм/мин
|
е≤5
|
1
|
Вырубка штампом-просечкой или
механическая обработка по ГОСТ 26277 и приложению К настоящего стандарта
|
100
|
5<е≤12
|
2
|
Вырубка штампом-просечкой
или механическая обработка по ГОСТ 26277 и приложению К настоящего стандарта
|
50
|
е>12
|
2
|
Механическая обработка по ГОСТ
26277 и приложению К настоящего стандарта
|
25
|
При
разногласиях образцы изготовляют механической обработкой.
При
изготовлении ось образца-лопатки должна быть параллельна оси трубы.
Перед испытанием
образцы кондиционируют при стандартной атмосфере 23 по ГОСТ 12423 не менее 2 ч.
При
расчете относительного удлинения при разрыве по изменению расстояния между
зажимами эквивалентную длину lэкв для образца типа 1 принимают
равной 33 мм, для образца типа 2—60 мм».
Пункт
8.8. Второй абзац. Заменить слово: «триметил-бензола» на «1, 3,
5-триметилбензола с содержанием основного вещества в указанных
компонентах≥95 %».
Пункты
8.9.2, 8.9.4 (последний абзац). Заменить слово: «трех» на «двух».
Пункт
8.10. Наименование дополнить словами: «—маломасштабным методом».
Пункт
8.10.3. Первый абзац. Заменить слово: «укороченных» на «ненагруженных»; после
слов «поверхность образца» дополнить словами: «в зоне инициирования»;
второй
абзац. Заменить слова: «при е>16 мм» на «при 16≤е<32
мм и (16±1) ч при е≥32 мм».
Пункт
8.10.5. Последний абзац. Заменить обозначение: Pе на Рс;
дополнить
абзацем:
«Допускается
определять стойкость к быстрому распространению трещин маломасштабным методом
при испытательном давлении, рассчитанном по таблице 2 для требуемого МОР.
Результат испытания считают положительным, если не происходит распространения
трещины — максимальная длина трещины а≤4,7d. При этом
критическое давление больше испытательного».
Пункт 8.11.
Таблицы 5, 6 (кроме примечаний) изложить в новой peдакции:
Таблица 5
В миллиметрах
Номинальный наружный
диаметр d
|
Остаточная толщина стенки еост
для труб
|
SDR
17,6
|
SDR
17
|
SDR
13,6
|
SDR
11
|
SDR
9
|
Мин.
|
Макс.
|
Мин.
|
Макс.
|
Мин.
|
Макс.
|
Мин.
|
Макс.
|
Мин.
|
Макс.
|
50
|
-
|
-
|
-
|
-
|
-
|
-
|
-
|
-
|
4,4
|
4,6
|
63
|
-
|
-
|
-
|
-
|
-
|
-
|
4,5
|
4,8
|
5,5
|
5,8
|
75
|
-
|
-
|
-
|
-
|
4,3
|
4,5
|
5,3
|
5,6
|
6,5
|
6,9
|
90
|
4,1
|
4,3
|
4,2
|
4,4
|
5,1
|
5,4
|
6,4
|
6,7
|
7,9
|
8,3
|
110
|
4,9
|
5,2
|
5,1
|
5,4
|
6,3
|
6,6
|
7,8
|
8,2
|
9,6
|
10,1
|
125
|
5,5
|
5,8
|
5,8
|
6,1
|
7,2
|
7,5
|
8,9
|
9,3
|
10,9
|
11,5
|
140
|
6,2
|
6,6
|
6,5
|
6,8
|
8,0
|
8,4
|
9,9
|
10,4
|
12,2
|
12,9
|
160
|
7,1
|
7,5
|
7,4
|
7,8
|
9,2
|
9,7
|
11,4
|
12,0
|
14,0
|
14,7
|
180
|
8,0
|
8,4
|
8,3
|
8,8
|
10,4
|
10,9
|
12,8
|
13,4
|
15,7
|
16,5
|
200
|
8,9
|
9,3
|
9,3
|
9,8
|
11,5
|
12,1
|
14,2
|
14,9
|
17,5
|
18,4
|
225
|
10,0
|
10,5
|
10,5
|
11,0
|
12,9
|
13,6
|
16,0
|
16,8
|
19,6
|
20,6
|
250
|
11,1
|
11,6
|
11,5
|
12,1
|
14,4
|
15,1
|
17,7
|
18,6
|
21,8
|
22,9
|
280
|
12,4
|
13,0
|
12,9
|
13.6
|
16,1
|
16,9
|
19,8
|
20,8
|
24,3
|
25,6
|
315
|
14,0
|
14,7
|
14,6
|
15,3
|
18,2
|
19,1
|
22,3
|
23,5
|
27,3
|
28,7
|
Таблица
6
SDR
|
Испытательное давление,
МПа
|
ПЭ 80
|
ПЭ 100
|
17,6
|
0,482
|
0,554
|
17
|
0,5
|
0,575
|
13,6
|
0,635
|
0,73
|
11
|
0,8
|
0,92
|
9
|
1,0
|
1,2
|
Раздел
8 дополнить пунктом – 8.12:
«8.12
Определение стойкости к быстрому распространению трещин полномасштабным методом
8.12.1
Аппаратура
Канал с
крышками (рисунок 5), предназначенный для размещения трубы длиной ≥14 м,
с системой воздушного термостатирования, обеспечивающей поддержание температуры
по всей длине испытуемой трубы в пределах (0 ±1,5) °С. По длине канала
устанавливают не менее четырех опор, исключающих прогиб трубы.
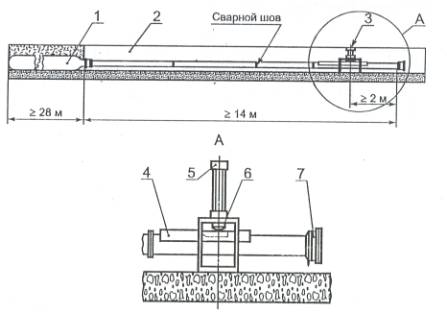
1 — стальной ресивер; 2 — канал; 3 —
приспособление для инициирования трещины; 4 — рама для охлаждения; 5 — пневматический цилиндр; 6
—лезвие; 7 — заглушка
Рисунок 5 — Схема установки для испытания полномасштабным методом на
стойкость к быстрому распространению трещин
Стальной
ресивер, минимальной длиной в два раза превышающей длину испытуемой трубы, и
объемом, в три раза большим объема испытуемой трубы. Внутренний диаметр
присоединительного участка ресивера должен иметь диаметр больший или равный
внутреннему диаметру испытуемой трубы.
Система
для создания давления с погрешностью ±2 % от заданного давления в испытуемой
трубе и стальном ресивере. В качестве среды испытания используют азот или
воздух.
Оборудование
для инициирования трещины, включающее:
- фрезу
для механической обработки продольной канавки на наружной поверхности трубы
шириной »10 мм, глубиной »80 % от номинальной толщины стенки трубы,
длиной »500 мм с
равномерным уменьшением глубины канавки до выхода ее на наружную поверхность
трубы в направлении стального ресивера на длине »250 мм (рисунок 6).
Длина трубы, на которой выполняется канавка, должна быть не менее 3 м. Центр
канавки с постоянной глубиной должен находиться на расстоянии не менее 2 м от
заглушаемого конца трубы;
Размеры в миллиметрах
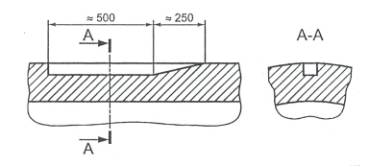
Рисунок
6 – Канавка, обрабатываемая на наружной поверхности трубы
-
приспособление для нанесения удара, инициирующего образование трещины в трубе,
состоящее из пневмоцилиндра и бойка в виде стального лезвия. Конструкция
лезвия, приводимого в движение быстродействующим поршнем пневмоцилиндра,
приведена на рисунке 7;
Размеры в миллиметрах

Рисунок
7 – Стальное лезвие для инициирования трещины в полиэтиленовой трубе
-
систему охлаждения верхней части трубы в зоне канавки смесью твердой двуокиси
углерода по ГОСТ 12162 с незамерзающей жидкостью, отвечающей требованиям ГОСТ
28084, состоящую из деревянного лотка длиной около 1 м, выложенного
полиэтиленовой пленкой для заполнения охлаждающей средой, и опирающегося на
верхнюю часть трубы (рисунок 8);
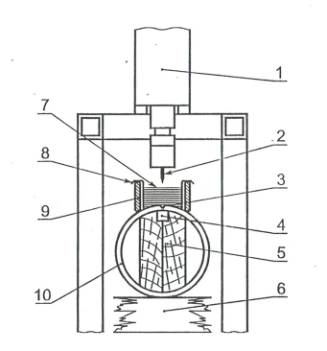
1 – пневмоцилиндр; 2 – лезвие; 3 – канавка; 4
– упругий материал; 5 – деревянная вставка; 6 - опора; 7 – охлаждающая
жидкость; 8 – полиэтиленовая пленка; 9 – деревянный лоток; 10 - испытуемая
труба
Рисунок
8 – Система охлаждения
- деревянную
вставку длиной 0,5 м, поддерживающую изнутри под канавкой испытуемую трубу и
предотвращающую ее деформацию в процессе инициирования трещины. Верхняя часть
вставки должна иметь углубление, которое заполняют упругим вспененным
материалом для того, чтобы фиксировать положение деревянной вставки по
отношению к канавке, в том числе при деформации трубы в процессе ее нагружения
испытательным давлением, а также обеспечить охлаждение всей толщины трубы под
канавкой, изолируя эту часть трубы от среды, подающей давление.
8.12.2
Подготовка к испытанию
На
испытуемой трубе обрабатывают канавку в соответствии с рисунком 6 и размещают
деревянную вставку под канавкой. При этом центр канавки должен находиться на
расстоянии не менее 2 м от конца трубы. На конец испытуемой трубы у канавки
устанавливают заглушку.
Прямые
отрезки труб сваривают встык для получения образца длиной не менее 14 м,
включая отрезок трубы с нанесенной канавкой, грат не удаляют.
Испытуемую
трубу помещают в канал, соединяют с металлическим ресивером, измеряют длину
трубы от центра инициирования до места соединения с ресивером рулеткой по ГОСТ 7502
и кондиционируют при (0±1,5) ºС в течение (6±0,5) ч при толщине стенки
трубы е<1б мм, (10±1) ч при 16≤е<32 мм и (16±1) ч при
е≥32 мм. Температуру измеряют с интервалом не более 2 м вдоль
любой стороны трубы от конца деревянной рамы к стальному ресиверу.
8.12.3
Проведение испытания
Испытуемую
трубу охлаждают в зоне инициирования трещины смесью твердой двуокиси углерода с
незамерзающей жидкостью до температуры минус 60 °С в течение не менее 1 ч.
Затем
создают давление в испытуемой трубе и ресивере с погрешностью ±2%, рассчитанное
по таблице 2 для требуемого МОР. Удаляют устройство для охлаждения канавки и
инициируют образование трещины ударом металлического лезвия, расположенного
вдоль канавки, по охлажденной канавке в центре ее полной глубины в месте
расположения деревянной вставки. Ход бойка должен обеспечивать прорезание
стенки трубы на длину лезвия (400 мм).
Удар
наносят не позднее чем через три минуты после нагружения трубы испытательным
давлением.
Затем
измеряют длину разрушенного участка трубы, включая длину трещины от центра ее
инициирования, рулеткой по ГОСТ 7502.
При этом трещина не должна заканчиваться на сварном шве. В этом случае образец
заменяют другим и испытывают вновь.
8.12.4
Обработка результатов
Рассчитывают
отношение длины разрушившегося участка в процентах к длине испытуемой трубы,
измеренной от центра инициирования трещины.
Результат
испытания считают удовлетворительным, если при испытательном давлении,
рассчитанном по таблице 2 для требуемого максимального рабочего давления МОР,
наибольшая длина разрушившегося участка меньше или равна 90 % от длины
испытуемой трубы.
Длина
разрушения трубы более 90 % длины испытуемой трубы, xaрактеризующая процесс
быстрого распространения трещин, является отрицательным результатом».
Пункт 9.2. Второй абзац. Заменить слова: «не более
3 м для SDR 17,6 и 4 м для SDR 11» на «не более 3 м для SDR 17, SDR 17,6 и 4 м
для SDR 13,6, SDR 11, SDR 9».
Приложение
А. Таблицу А. 1 изложить в новой редакции:
Таблица
А.1
Максимальное рабочее
давление МОР, МПа
|
Расчетное значение
коэффициента запаса прочности С для максимального рабочего давления МОР
|
Трубы из ПЭ 80 (MRS 8,0
МПа)
|
Трубы из ПЭ 100 (MRS 10,0
МПа)
|
SDR
17,6
|
SDR
17
|
SDR
13,6
|
SDR
11
|
SDR
9
|
SDR
17,6
|
SDR
17
|
SDR
13,6
|
SDR
11
|
SDR 9
|
0,3
|
3,2
|
3,3
|
4,2
|
5,3
|
6,7
|
4,0
|
4,2
|
5,3
|
6,7
|
8,3
|
0,4
|
2,4
|
2,5
|
3,2
|
4,0
|
5,0
|
3,0
|
3,1
|
4,0
|
5,0
|
6,2
|
0,6
|
-
|
-
|
2,1
|
2,7
|
3,3
|
2,0
|
2,1
|
2,6
|
3,3
|
4,2
|
1,0
|
-
|
-
|
-
|
-
|
2,0
|
-
|
-
|
-
|
2,0
|
2,5
|
1,2
|
-
|
-
|
-
|
-
|
-
|
-
|
-
|
-
|
-
|
2,1
|
Приложение Б исключить.
Приложение
В. Таблицу В.1 (кроме примечаний) изложить в новой редакции:
Таблица
В.1
Номинальный наружный
диаметр d, мм
|
Расчетная масса 1 м труб,
кг
|
SDR
17,6
|
SDR
17
|
SDR
13,6
|
SDR 11
|
SDR 9
|
20
|
-
|
-
|
-
|
0,132
|
0,162
|
25
|
-
|
-
|
-
|
0,169
|
0,210
|
32
|
-
|
-
|
0,229
|
0,277
|
0,325
|
40
|
0,281
|
0,292
|
0,353
|
0,427
|
0,507
|
50
|
0,436
|
0,449
|
0,545
|
0,663
|
0,790
|
63
|
0,682
|
0,715
|
0,869
|
1,05
|
1,25
|
75
|
0,970
|
1,01
|
1,23
|
1,46
|
1,76
|
90
|
1,40
|
1,45
|
1,76
|
2,12
|
2,54
|
110
|
2,07
|
2,16
|
2,61
|
3,14
|
3,78
|
125
|
2,66
|
2,75
|
3,37
|
4,08
|
4,87
|
140
|
3,33
|
3,46
|
4,22
|
5,08
|
6,12
|
160
|
4,35
|
4,51
|
5,50
|
6,67
|
7,97
|
180
|
5,52
|
5,71
|
6,98
|
8,43
|
10,1
|
200
|
6,78
|
7,04
|
8,56
|
10,4
|
12,5
|
225
|
8,55
|
8,94
|
10,9
|
13,2
|
15,8
|
250
|
10,6
|
11,0
|
13,4
|
16,2
|
19,4
|
280
|
13,2
|
13,8
|
16,8
|
20,3
|
24,4
|
315
|
16,7
|
17,4
|
21,3
|
25,7
|
30,8
|
Приложение
Г. Таблицу Г.1 изложить в новой редакции:
Таблица
Г.1
Номинальный наружный
диаметр, мм
|
ПЭ 80
|
ПЭ 100
|
SDR 17,6
|
SDR
17
|
SDR
13,6
|
|
SDR
9
|
SDR
17,6
|
SDR
17
|
SDR
13,6
|
SDR
11
|
SDR
9
|
20
|
-
|
-
|
-
|
2248118901
|
2248118501
|
-
|
-
|
-
|
2248119101
|
2248118551
|
25
|
-
|
-
|
-
|
2248118902
|
2248118502
|
|
-
|
-
|
2248119102
|
2248118552
|
32
|
-
|
-
|
2248118703
|
2248118903
|
2248118503
|
-
|
-
|
-
|
2248119103
|
2248118553
|
40
|
2248118804
|
2248118604
|
2248118704
|
2248118904
|
2248118504
|
-
|
-
|
2248118754
|
2248119104
|
2248118554
|
50
|
2248118805
|
2248118605
|
2248118705
|
2248118905
|
2248118505
|
2248119005
|
2248118655
|
2248118755
|
2248119105
|
2248118555
|
63
|
2248118806
|
2248118606
|
2248118706
|
2248118906
|
2248118506
|
2248119006
|
2248118656
|
2248118756
|
2248119106
|
2248118556
|
75
|
2248118807
|
2248118607
|
2248118707
|
2248118907
|
2248118507
|
2248119007
|
2248118657
|
2248118757
|
2248119107
|
2248118557
|
90
|
2248118808
|
2248118608
|
2248118708
|
2248118908
|
2248118508
|
2248119008
|
2248118658
|
2248118758
|
2248119108
|
2248118558
|
110
|
2248118809
|
2248118609
|
2248118709
|
2248118909
|
2248118509
|
2248119009
|
2248118659
|
2248118759
|
2248119109
|
2248118559
|
125
|
2248118810
|
2248118610
|
2248118710
|
2248118910
|
2248118510
|
2248119010
|
2248118660
|
2248118760
|
2248119110
|
2248118560
|
140
|
2248118811
|
2248118611
|
2248118711
|
2248118911
|
2248118511
|
2248119011
|
2248118661
|
2248118761
|
2248119111
|
2248118561
|
160
|
2248118812
|
2248118612
|
2248118712
|
2248118912
|
2248118512
|
2248119012
|
2248118662
|
2248118762
|
2248119112
|
2248118562
|
180
|
2248118813
|
2248118613
|
2248118713
|
2248118913
|
2248118513
|
2248119013
|
2248118663
|
2248118763
|
2248119113
|
2248118563
|
200
|
2248118814
|
2248118614
|
2248118714
|
2248118914
|
2248118514
|
2248119014
|
2248118664
|
2248118764
|
2248119114
|
2248118564
|
225
|
2248118815
|
2248118615
|
2248118715
|
2248118915
|
2248118515
|
2248119015
|
2248118665
|
2248118765
|
2248119115
|
2248118565
|
250
|
2248118816
|
2248118616
|
2248118716
|
2248118916
|
2248118516
|
2248119016
|
2248118666
|
2248118766
|
2248119116
|
2248118566
|
280
|
2248118817
|
2248118617
|
2248118717
|
2248118917
|
2248118517
|
2248119017
|
2248118667
|
2248118767
|
2248119117
|
2248118567
|
315
|
2248118818
|
2248118618
|
2248118718
|
2248118918
|
2248118518
|
2248119018
|
2248118668
|
2248118768
|
2248119118
|
2248118568
|
Приложение
Д. Таблица Д.1. Графу «Метод испытания» для показателя 1 после слова «разделы»
дополнить ссылкой: 4.
Приложение
Е. Пункт Е.2 изложить в новой редакции:
«Е.2
Контрольные образцы внешнего вида поверхности трубы оформляют на один типовой
представитель от каждой группы труб по диаметрам в соответствии с 7.2, и они
являются контрольными образцами для всех стандартных размерных отношений SDR
группы».
Приложение
Ж. Пункт Ж. 1 дополнить примечанием (после пятого абзаца):
«Примечание — При испытании на
термостабильность после облучения с отрезков труб перед изготовлением
испытуемых образцов снимают поверхностный слой (стружку) толщиной 0,2 мм».
Приложение
Л. Наименование. Исключить ссылки: «[1] и [2]»;
таблицу
Л.1 изложить в новой редакции:
Таблица
Л.1
По ГОСТ Р 50838
|
По техническим условиям
|
ПЭ 80
|
ПЭ 80Б-275, ПЭ 80Б-286 [1]
PE6GP-26B
[2]
F
3802Y, F 3802YCF [3]
F 3802В [4]
|
ПЭ 100
При освоении производства
или закупке по импорту
|
—
|
Приложение
М. Позицию [1] изложить в новой редакции:
«[1] ТУ
2243—046—00203521—2004 Композиция полиэтилена средней плотности для труб и
соединительных деталей газораспределительных сетей марок ПЭ80Б-275 и
ПЭ80Б-286»;
позиция
[2]. Заменить обозначение: ТУ 6—11—00206368—25—95 на ТУ 6-11-00206368-25-93;
дополнить
позицией — [4]:
«[4] ТУ
2211-007-50236110-2003 Полиэтилен средней плотности марки F 3802В для
трубопроводов».
(ИУС № 12 2004 г.)
Вернуться в основной документ
Источник информации: https://internet-law.ru/stroyka/text/6368/index9278.htm
На эту страницу сайта можно сделать ссылку:
На правах рекламы:
|